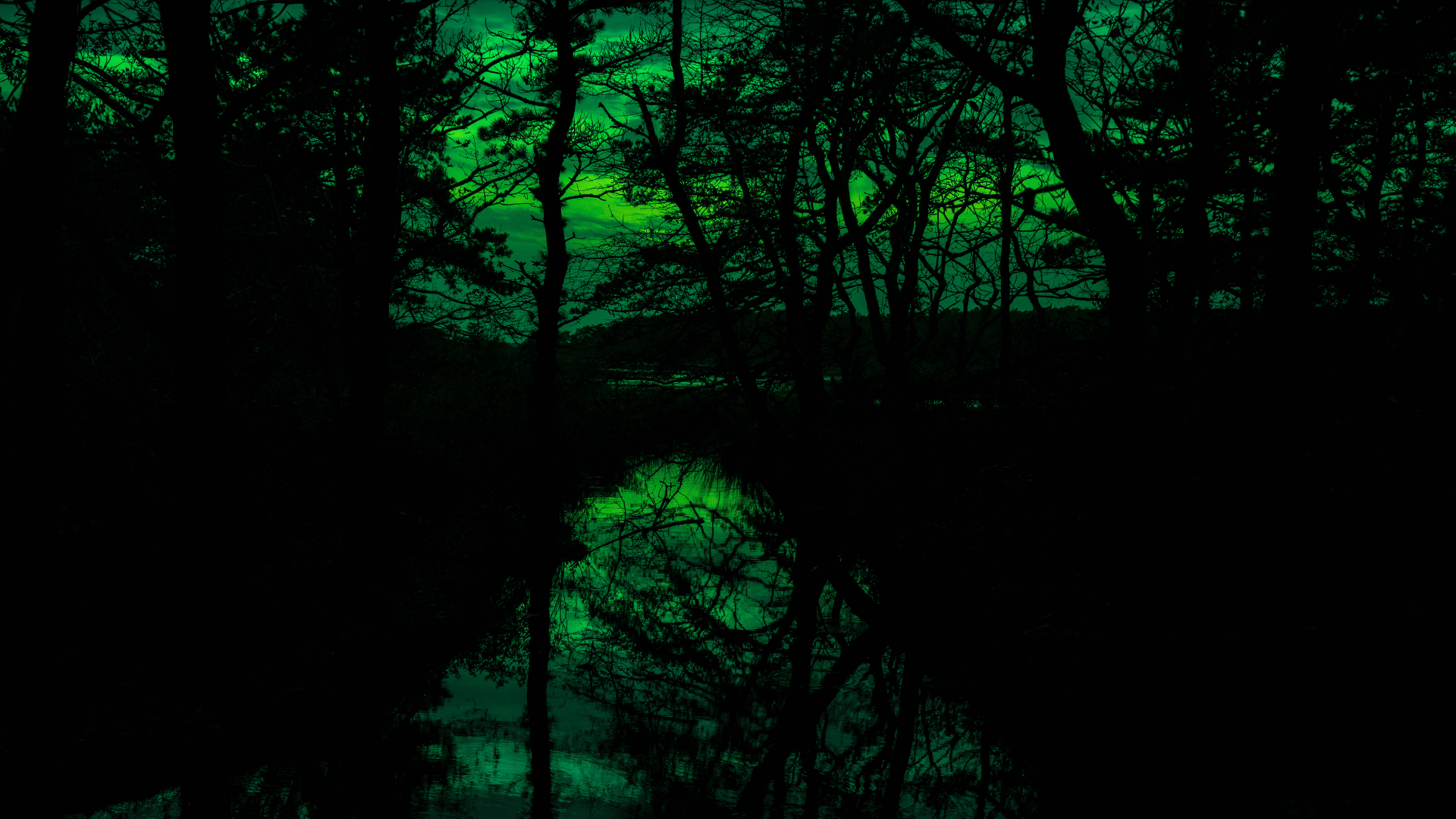
Glossary Definition
Active Infrared Thermography: Illuminating Invisible Thermal Information
Active Infrared Thermography is a powerful non-destructive testing (NDT) technique that utilizes the principles of infrared thermography to analyze and inspect materials and objects. Unlike passive infrared thermography, which relies on the natural heat emissions of objects, active infrared thermography actively introduces thermal excitation into the material being examined. By applying controlled heat or thermal energy to the surface and monitoring the resulting temperature changes, active infrared thermography reveals hidden flaws, defects, or anomalies that may not be visible to the naked eye.
How Active Infrared Thermography Works:
- Thermal Excitation: In active infrared thermography, an external energy source, such as a heat lamp, flash lamp, or laser, is used to provide thermal excitation to the material’s surface. This causes localized heating and induces a thermal gradient within the material.
- Thermal Imaging: A high-resolution infrared camera is then employed to capture the infrared radiation emitted by the heated surface. The camera detects the temperature variations, converting them into thermal images or thermograms.
- Image Analysis: The thermograms obtained during the active infrared thermography process reveal patterns of heat distribution and temperature changes on the surface. These patterns are influenced by the internal structure and properties of the material.
- Defect Detection: By analyzing the thermal images, experts can identify defects, delaminations, cracks, voids, corrosion, or other irregularities within the material. Areas with defects typically exhibit distinct temperature variations compared to the surrounding regions.
Applications of Active Infrared Thermography:
Active Infrared Thermography finds widespread application in various industries and fields, including:
- Aerospace and Aviation: Active infrared thermography is used to inspect aircraft components, such as wings, fuselage, and engine parts, for hidden defects or damage, ensuring airworthiness and safety.
- Manufacturing and Quality Control: In manufacturing processes, active infrared thermography helps detect defects in composite materials, ceramics, plastics, and metallic components, ensuring the quality and integrity of products.
- Civil Infrastructure: The technique is applied to assess the structural health of bridges, buildings, and concrete structures, enabling early detection of flaws and facilitating maintenance efforts.
- Automotive Industry: Active infrared thermography is used to inspect automotive parts for flaws or defects during production, improving vehicle safety and performance.
- Archaeology and Art Restoration: Active infrared thermography is employed to examine artworks, paintings, and archaeological artifacts for hidden layers, damage, or signs of restoration, without physical intervention.
Advantages of Active Infrared Thermography:
- Non-Destructive Testing: Active infrared thermography is non-destructive, meaning it does not damage the material or object under examination.
- Rapid Inspection: The technique allows for quick and efficient inspection of large areas, reducing downtime and inspection costs.
- Wide Range of Materials: Active infrared thermography can be applied to a wide range of materials, including metals, composites, ceramics, and polymers.
- Early Detection of Defects: Active infrared thermography enables early detection of defects, helping prevent catastrophic failures and ensuring safety.
Conclusion:
Active Infrared Thermography is a valuable tool for non-destructive testing, enabling the detection of hidden defects and anomalies in various materials. By actively inducing thermal excitation and analyzing resulting temperature changes, active infrared thermography provides crucial insights into the integrity and quality of materials used in industries ranging from aerospace to art restoration. Its non-invasive nature, rapid inspection capabilities, and ability to reveal invisible thermal information make it an indispensable technique for ensuring safety, performance, and reliability in diverse applications.